物流現場を改善したい
多様な業種業態を対象に改善活動を展開
自動化オペレーションの現場づくりにも対応
お客様の物流改善活動をサポート
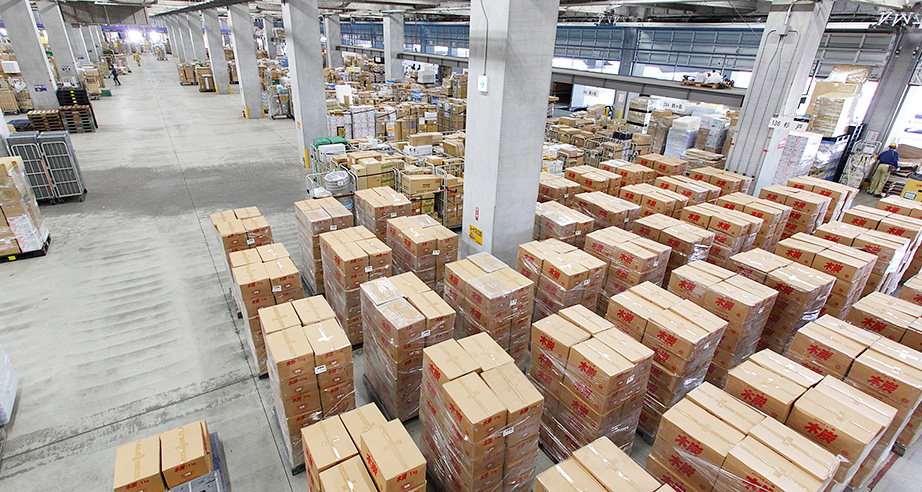
「限られた倉庫スペースを有効に使いたい」「スタッフに負担が掛からず、かつ効率のいい作業動線を構築したい」「物量波動に柔軟に対応できる勤務シフトを組みたい」「物流施設の運営コストを低く抑えたい」−−−−物流現場には、こうした課題やニーズが山積しているものの、まず何から手をつければいいのか、解決に向けた取り組みは本当に正しいのか。自社独自で展開する改善活動に不安を感じることはありませんか?
そのような場合には、作業生産性の向上につながる物流現場づくりや改善活動の支援を得意としている当社に、是非ともお声掛けください。
自社事業所での改善活動はもちろんのこと、サプライチェーンの上流工程から下流まで、様々な業種業態のお客様の物流現場において改善活動をサポートしてきた実績があり、ノウハウも豊富です。過去の取り組みは、物流関連団体での受賞歴があるなど、外部からも高く評価されています。
現状分析から改善プラン提案・実行まで
既存の庫内オペレーションにはどのような課題があるのか。当社の専門スタッフが物流現場に何度も足を運び、問題箇所を洗い出します。続いて、現状分析の結果に基づき、具体的な改善プラン(あるべき姿)をご提案します。その後、プランの実行、効果検証などを経て、新たな仕組みを物流現場に定着させていきます。
従来は人手の活用に焦点を当てた改善活動を展開する物流現場が少なくありませんでした。しかし近年は、労働力不足を背景に、機械化や自動化の設備を取り入れるかたちでの物流現場の再構築を志向するお客様が増えつつあります。そのため、当社では、各種マテハン機器や物流ロボットなど最新鋭のテクノロジーを用いた物流現場づくりにも対応しています。
当社およびSBSグループ各社における物流現場改善プロジェクトの取り組み事例は以下のページよりご覧いただけます。
全国の支店・営業所で実行された物流現場改善事例
支店・チーム名 | 改善活動のテーマ | 活動内容と成果 |
---|---|---|
土浦支店 CDC検収チーム |
物流センターの印象品質改善 |
物流センターに納品で訪れるドライバーをお客様として、現状の不満やニーズを聴き、次々と改善。荷主のファンを物流センターでも作ろうというユニークな挑戦。 |
土浦支店 中貫DCチーム |
納品台車管理システムの構築による事務所作業時間の短縮
全日本物流改善事例大会2011 物流合理化努力賞 受賞! |
納品台車の取り違え防止・配送後の納品台車管理の事務負担軽減を、なんと29,800円のレジスターで実現。 |
小山支店 構内部門チーム |
人員配置の適正化と 作業改善 |
日々の出荷量に応じて作業人員を適正配置化。バラ商品のピッキング方法を変更。物流センターの作業生産性を高め、人件費などコストダウンに成功。 |
土浦支店 中貫DCチーム |
出荷物量のJIT化による 在庫スペース抑制 全日本物流改善事例大会2010 物流合理化賞 受賞! |
特売品の見込み発注と荷受けで在庫保管スペースが不足していたが、ベンダーに必要な分だけを追加で納品してもらうようにすることで製品在庫と保管スペースを大幅に削減できた。 |
新宿支店 本館プラットチーム |
フロア別集荷による 生産性向上 |
百貨店店舗のテナントからの集荷を、利用納品代行業者別からフロア別に切り替えることで、作業員の生産性向上を実現した。 |
早稲田営業所 | 業務の数値化による 必要作業員数の適正化 |
適正な作業人員を投入するために日々業務の数値化に着手した。 |
日野営業所 配送チーム |
自社車両稼働率の向上 | 傭車比率の見直しとドライバー助手の社員→アルバイト化に取り組んでコストダウンを実現。営業所の収益改善に成功した。 |
向島支店 構内チーム |
作業人員配置の適正化と 作業レーン見直しによる 生産性向上 |
出荷量の曜日波動に応じた作業員の適正配置と作業レーンの見直しに着手。その結果、業務の平準化などに成功し作業生産性が向上した。 |
厚木支店 1F&2F入出荷チーム |
進捗状況の共有化による 作業生産性向上 |
ホワイトボードなどを活用して作業の進捗状況や結果を「見える化」。作業員個々のやる気を引き出して生産性向上を実現した。 |
東扇島支店 TCチーム |
作業スタート時間調整による生産性向上 | 仕分けシュート下での作業が本格的に動き出す時間帯に合わせて必要な数のスタッフを投入することで、手待ち状態をなくして作業生産性を向上させた。 |
東扇島支店 DCチーム |
商品破損事故の削減 | オリコンの仮置き方法見直しやひな壇取りの禁止、割れ物商品のロケーション変更などを通じて商品破損事故の発生件数を削減した。 |
東扇島支店 低温チーム |
DAS作業の見直しによる 作業生産性の向上 |
DAS(デジタルアソートシステム)を使った仕分け作業の進め方にメス。動線変更やシステム運用方法見直し、作業員への指導などを通じて生産性向上に成功した。 |
東扇島支店 輸送チーム |
配送ルートのマニュアル化による燃料費削減 | ドライバー任せだった納品時の走行ルート、帰庫ルートをマニュアル化。トラックの走行距離を減らすことで、使用する燃料のコストを削減した。 |
郡山営業所 | ルート輸送体制確立による コスト削減 |
積載効率が悪いままオーダーごとにトラックを配車していたのを改め、積み合わせ輸送を実施することで輸送コスト削減に成功した。 |
東京貨物ターミナル営業所 | 集荷作業の生産性・品質の向上 | パレタイズの工夫とバラ積みの実行によって1コンテナ当たりの積載ケース数をアップした。 |
川崎支店 | ドライバーの勤務ローテーション変更によるコスト削減 | 完全週休2日制を前提にした勤務ローテーションに改めて休日出勤を是正し、人件費の削減などに成功した。 |
横浜町田支店 | 運行三費の削減 | 配送ルート設定上、可能な場合は自社タンクを保有する隣接支店での給油に切り替えることで燃料費を削減した。 |
君津支店 | ドライバー教育を通じたエコドライブ徹底による燃費向上 | エコドライブ講習の受講やデジタコを活用したドライビング状況の把握などによってドライバーに省エネ運転を徹底。配送トラックの燃費向上を実現した。 |
海運支店 | センター運営見直しによるコスト削減 | 庫内レイアウト、棚番の整理、ABC分析などを実行することで、センターオペレーションの生産性を向上させた。 |
こんな物流改善も...
現場のアイデアから生まれたツール。ほんの少しの工夫も、積み重ねて大きな効果を発揮!
パートさんのアイデアも、積極的に取り入れています。
シャトルプリンター
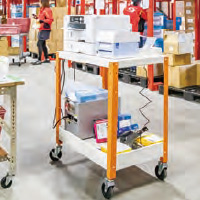
通路で積み方研修
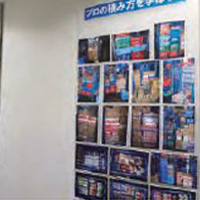
受付表の掲示
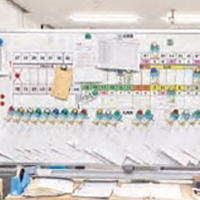
仕分け表示板
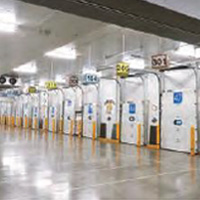
歩車道の分離
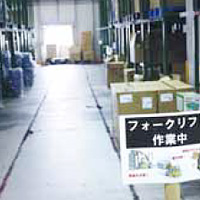
棚に商品を直接陳列
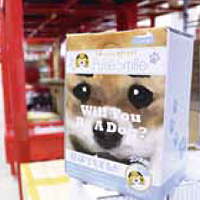
品質向上のための取り組み

物流現場の品質・安全・生産性向上を目指して、専門組織「品質管理室」を2022年01月に発足しました。全国各地の支店・営業所の取り組みを定期的にチェック・改善し、全社的なレベルアップを図るべく活動を行っています。詳細は以下のリンクよりご覧ください。